- Introduction
- People
- Research Area
- Projects
- Services
- Facilities
- Achievements
- Gallery
- Contact
‘Special products development’ value chain at CMTI encompasses end-to-end solutions involving Design, Manufacture, Quality Control, Assembly, Testing & Validation and Installation & Commissioning. The Central Manufacturing Facility (CMF) has a team of engineers and scientists having comprehensive experience in product development and caters to sponsored and R&D projects in manufacturing technology. CMF is the hub of manufacturing activities in CMTI.
Centre Head | |||
Photo | Name | Designation | View Profile |
---|---|---|---|
![]() |
Dr. Nagahanumaiah | Director | View Profile |
Group Head | |||
Photo | Name | Designation | View Profile |
---|---|---|---|
![]() |
Mr. Raju V R | Scientist - E | View Profile |
Scientists | |||
Photo | Name | Designation | View Profile |
---|---|---|---|
![]() |
Mr. Bharath P | Scientist - D | View Profile |
![]() |
Mr. Vignesh Kemminje | Scientist - C | View Profile |
Technical Staff | |||
Photo | Name | Designation | Phone (Office) |
---|---|---|---|
![]() |
Mr. Adesh Jain N | Technical Officer A | 080-22188333 |
![]() |
Mr. Anandareddy R | Technical Officer A | 080-22188333 |
![]() |
Mr. Harish M | Senior Technical Assistant - II | 080-22188257 |
![]() |
Mr. Shiva Kumar M | Senior Technical Assistant - I | 080-22188238 |
![]() |
Mr. Raghu R | Senior Technical Assistant - I | 080-22188269 |
![]() |
Mr. Thimmaraju | Technician III | 080-22188238 |
![]() |
Mr. Venkatesha G | Technician III | 080-22188238 |
![]() |
Mr. Santhosha B R | Technician III | 080-22188238 |
![]() |
Mr. Manjunatha D B | Technician III | 080-22188269 |
![]() |
Mr. Satish Kumar S | Technician III | 080-22188238 |
![]() |
Mr. Krishnakumara T | Technician III | 080-22188238 |
![]() |
Mr. Sagar K | Technician II | 080-22188238 |
![]() |
Mr. Harishkumar G | Technician II | 080-22188269 |
![]() |
Mr. Santhosh N S | Technician II | 080-22188238 |
Administration | |||
Photo | Name | Designation | Phone (Office) |
---|---|---|---|
![]() |
Mr. Balachandra S | MTA IV | 080-22188238 |
Central Manufacturing Facility(CMF) has carried out manufacturing related Research and Development projects in collaboration with industries and Academia. CMTI were pioneers in development of cutting tools for metal cutting operation and have developed many technologies for metal cutting. Some of the recent R&D activities carried out by CMF in the recent years include:
List of completed projects | |||
---|---|---|---|
Sl. No. | Name | Photo | Description |
|
Cryogenic machining (Cryogenics as a alternative to flood coolant) |
![]() ![]() |
Supply of Cryogenics such as Liquid Nitrogen (LN2 @ -196 °C) to the cutting zone is one research area that is being explored to improve the process efficiency of difficult to machine materials. Outcomes: Improvement in tool life reported. Subsequent applications found in machining of Tyre treads by Cryo machining for M/s. Ceat Tyres Ltd. |
|
Minimum Quantity Lubication(MQL) |
|
A collaborative R&D project carried out at CMTI with University of Arkansas – UARK, USA, to establish, using of MQL for manufacturing and to introduce this technology to the INDIAN manufacturing industry. Outcomes: The test results showed that nanoparticle integrated lubricants significantly reduce the cutting forces by reducing sliding friction between the tool and the work piece, increases Grinding-ratio and surface finish of the work pieces and improve the overall grinding performance in MQL applications compared to that with base fluids and conventional flood lubrication |
Other R&D projects carried out include
- Cutting Force measurements and Analysis for Spheroidal Grey Cast Iron during Turning and Drilling
- High Speed Machining of Stainless Steel
- Machining Technology development for Magnesium alloy, Aerospace components
Product manufacturing department manufactures components of high precision and special purpose applications. Some of the components manufactured in the past include the following
S. No. | Name | Photo |
---|---|---|
1 | Manufacturing and development of Armature coil Die set
Customer:MICO |
![]() |
2 | Hydraulic Filter components (Aerospace applications)
|
![]() |
3 | Precision Ball Screws (AeroSpace applications)
|
![]() |
4 | Manufacturing of Turbo blowers and Propellers (Aerospace applications)
|
![]() ![]() |
5 | Agitators
|
![]() ![]() |
Integrated Manufacturing Services
CAD/CAM
- CAD/CAM services in NX12/NX7.5 and Hypermill2019.2.
- CNC program generation for precision components and assemblies
- Interface between Process planning and CNC part programming
- Interface between process planning and operation Layout creation
- Jigs & Fixture design solutions
Manufacturing R&D
- Development of technology for novel materials etc.
- Solving complex manufacturing problems of Industry
- Methods Study
- Non-traditional machining like Die-sinking EDM and wire-cut EDM Laser machining
- Research streams from ongoing projects to facilitate PG projects for the academic fraternity.
- Re-conditioning of critical machine tool elements.
Manufacturing Planning Applications
- Selection of machine tools and manufacturing systems
- Technology Auditing and Productivity improvements
- Training programs in CAD/CAM NX-12 and NX-7.5 and training programs in manual part programming
- Preparation of Detailed Project report for product manufacture
- Process Planning and Time Estimation for Components
- Development of Machining Data Bank
Central Manufacturing Facility(CMF) workshops are equipped with the following machine tools:
- Universal milling machine
- Dual palette for quick set of components
- High-Pressure Coolant Through Spindle
- Swivel head repeatability: 0.001
- Spindle Run Out: 0.003 mm
- Positional accuracy: 0.005mm
- Rotary table accuracy :5arc sec
- Spindle RPM max: 18000
Work space: 1250X510X560 C Axis: 360º
Controller: Sinumerik 840D
- High torque spindle (High depth of cut)
- Dual palette
- Spindle RPM:10000
- Positional accuracy:0.01mm
- Repeatability: 0.005mm
- Positional Tolerance :6 arc sec
- Repeatability max: 3 arc sec
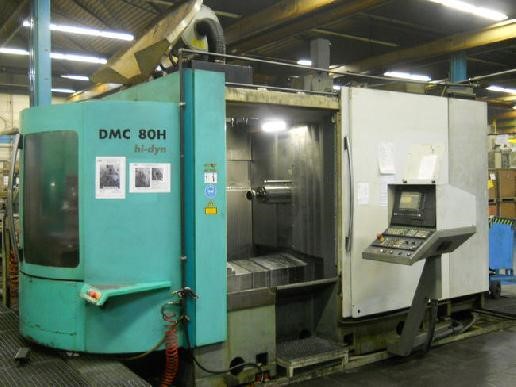
800X710X710
Sinumerik 840D
- Probe For Work Offset Measurement
- Laser For Tool Offset Measurement
- Parallel programming is possible High-Pressure Coolant Through Spindle
- Spindle speed: 18000 RPM
- Spindle taper: HSK 63A
- Rapid traverse: 60m/min (X and Y-Axis)
- Rapid traverse: 40m/min (Z-Axis)
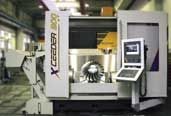
1200X1000X600 A:-30˚ to -110˚ C:360˚
Sinumerik 840 D
- Precision boring machine
- Table load capacity upto 1.5Ton
- Spindle RPM max:1800
- Spindle taper: ISO 50
1250X1100X940 W:630mm
Sinumerik 840 D
- Blum Touch probe
- Universal milling machine
- Spindle speed range: 31.5-3150 RPM
- Rotary table: C -Axis

630X500X460
Seimens 810D
- Spindle Speed: 80-8000 RPM
- Table working area-510mm X1000mm
- Table travel: 800mm (X- axis)
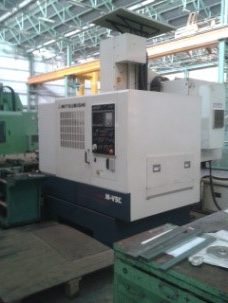
810X510X460
Fanuc
- Speed Range :100 – 4000
- Rapid traverse:15m/min(cross) 20m/min(transverse)
- Positioning accuracy : +/- 0.012 mm/30mm
- Repeatability:+/- 0.003 mm
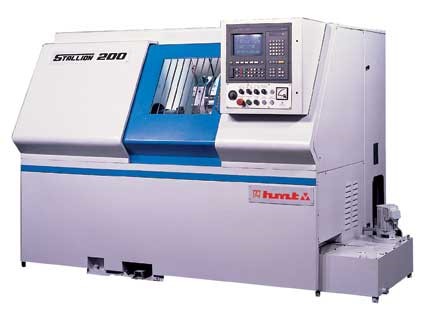
Swing over bed:460 Center distance: 440
Fanuc
- Angular machining
- Spindle speed: 7000/3500 RPM
- Number of tools: 15
- X-Axis travel: 1016mm
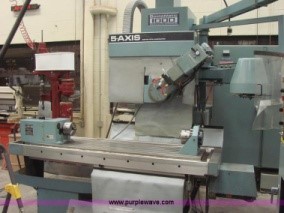
1016X432X432 A:360˚ B:±100˚
Sinumerik 840D
- Spindle speed range: 20- 6300
- Spindle runout: 0.003 mm
- Positional accuracy: 0.007
- Rotary axis accuracy: 9 arc sec
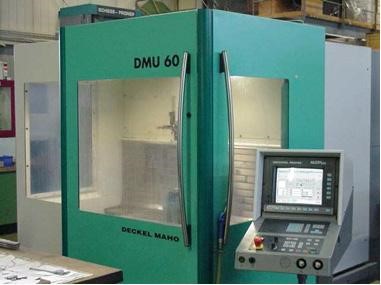
600X525X500
Heidenhein TNC 430
- Live C axis and servo turret
- Spindle speed range:40-4000 RPM
- Turret indexing accuracy 3 arc sec.
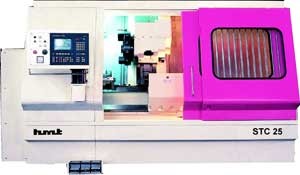
Swing over carriage:250 Center distance: 1000
FANUC
- Spindle speed range : 0-3000
- Spindle taper: MT-5
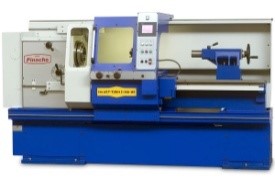
Swing over bed:300 Center distance: 1000
Fanuc
- Speed range : 35- 6000
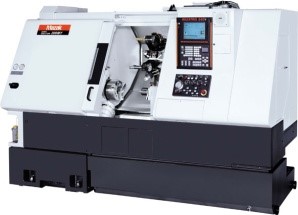
430X300
Mazatrol TPL
- Spindle speed range: 35-10000 RPM
- Rapid traverse X and Y axis 30m/min
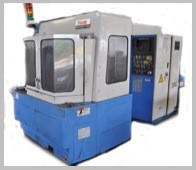
560X510X510
Mazatrol
- Spindle speed rate: 40-4000
- X axis and Y axis traverse :24m/min
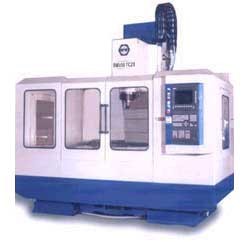
1020X510X560
Mazatrol Seimens 810D
- Spindle speed rate: 4000 RPM
710X500X500
Seimens 840D
- Spindle speed range: 1-6000 RPM
- No. of turret stations :12
- Accuracies X & Z axes :0.005mm
- pindle runout: 0.001mm
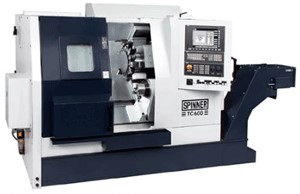
Max. Swing:450 Max. length:580
Sinumerik 810D
-
- Maximum helix angle:40deg right or left
- Wheel dimension: 350X160X8/10/12/20 mm
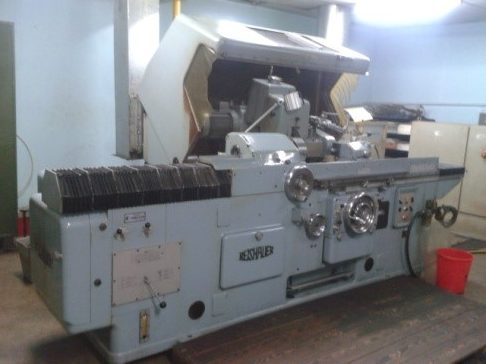
- Grinding length: 900 mm
- Admit between centers:1190 mm
- Smallest job dia: 10mm
- Greatest work diameter: 150mm
- Length positioning unit
- Dynamic balancing unit
- Air gap sensing unit
- Pictorial programming
- Universal wheel/work head
- Speed range:1- 1500 rpm
- Fitting taper :MT-5
- Roundness accuracy: 0.0004 mm
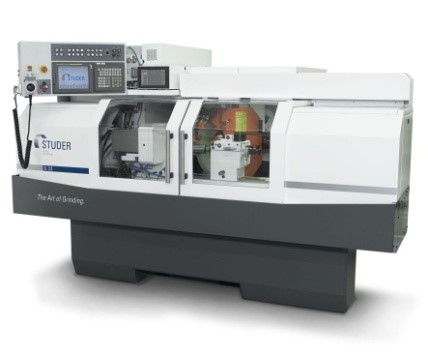
- Dist. Between centers: 1000 mm
- Center height:175 mm
- Dist. Between centers :1000 mm
- X-axis Max. travel: 286 mm Feed: 0.001- 5000 mm/min Resolution : 0.0001 mm
- Z-axis Max. travel: 1150 mm Feed : 0.001- 10000 mm/min Resolution:0.0001 mm
Fanuc 21i-TB
- Work head swivel:0-90 deg
- Spindle Nose Taper MT-5
- Collets Diameter:1-25mm
- Grinding wheel specification:400X50X127, 400X40X127
- Max. work Weight: 80kg
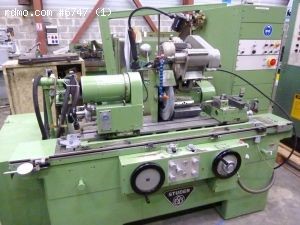
- Center Height: 125mm
- Distance Between Centers: 700mm
- Table Traverse Maximum: 700mm
- Vertical movement of wheel: 470mm
- Wheel specification: 300X50/40X127mm
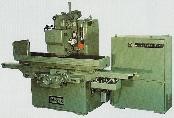
- Length Of Loading Surface: 1050mm
- Width of the loading surface: 240mm
- Grinding length: 1000mm
- Grinding width: 270mm
- Work spindle bore diameter: 50mm
- Spindle nose taper: Metric 70
- Maximum work head swivel: 30degree
- Maximum table travel: 600mm
- Spindle speed:3600 – 40000 rpm
- Center height: 180mm
- Maximum work piece length: 1000mm
- Grinding dia: 5 –200mm
- Measurement Resolution: 0.001 mm
- Available wire guide: 0.1 mm, 0.2 mm, 0.25 mm
- Wire Material :Brass
- Dielectric used : De-ionized water
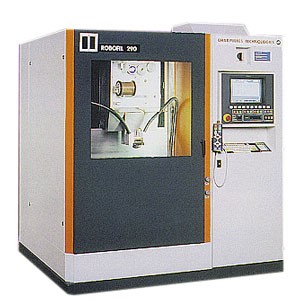
- X-axis :400 mm
- Y-axis :250 mm
- U-axis :400 mm
- V-axis :250 mm
- Z-axis :200 mm
- Max. Table work load :200 kg
- Max. Ram work load :25 kg
- X/y/Z positional variation: 0.02/100 mm
- Resolution: 0.001mm
- Material removal rate
- Copper:450.mm3/min
- Graphite:590 mm3/min
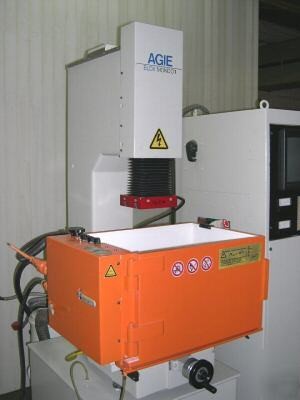
- X-axis :300 mm
- Y-axis :250 mm
- Z-axis :250 mm
Apart from these CMF is equipped with precision Tool room lathes, Gear Hobbing facility (Upto 5 Module). CMF is also equipped stationary 3 axis Tool force dynamometers used for measurement of cutting forces for R&D applications
- Manufacture and Supply of Propellers for aerospace sector.
- Manufacture and Supply of Precision slideways and spindle components for aerospace application.
Mr. Raju V R
Group Head – Central Manufacturing Facility
Central Manufacturing Technology Institute
Tumkur Road, Bengaluru - 560 022
Phone (Office): +91-80-22188297
Mobile: +91-9449842695
Fax: +91-80-23370428
E-mail: rajuvr[at]cmti[dot]res[dot]in