- Introduction
- People
- Research Areas
- Projects
- Achievements
- Gallery
- Contact
CMTI is pioneer in the field of Manufacturing has been mandated by DHI under the SAMARTH Udyog Bharat 4.0 Platform to set up a Smart Manufacturing Demo & Development Cell as a Common Engineering Facility Centre (CEFC) to propagate and support the process of adoption of smart manufacturing practices by the rapidly growing Indian manufacturing industry. CMTI is one of the nodal agency of Samarth Udyog (https://www.samarthudyog-i40.in/) established by the Department of Heavy Industry (DHI). Under this scheme, there is a provision for the Indian industry (as industry partner) to develop technology solutions/product development in collaboration with CMTI, mainly in the domain of Smart Manufacturing/Industry 4.0. In addition, the facilities are available for tryouts. SMDDC provides an excellent opportunity for Large scale manufacturers, MSME and Academia to collaborate in technology solutions activities related to smart manufacturing and Industry 4.0. The Major on-going activities of the centre are;
- Pilot implementation of ‘Smart manufacturing Demo cum Development Cell for Machine Tools’ at CMTI (Experience Centre - Awareness & Propagation) & Platform for development (Technology driver)
- Technology development, demonstration, trials, training, experience of learning, testing & validation of I4.0 products (R&D & Best practices)
- Customization & rollout of smart manufacturing solutions for MSMEs (Enabling localization & customised Implementation, Handholding)
- Industry Employable Manpower (Skilling & Reskilling)
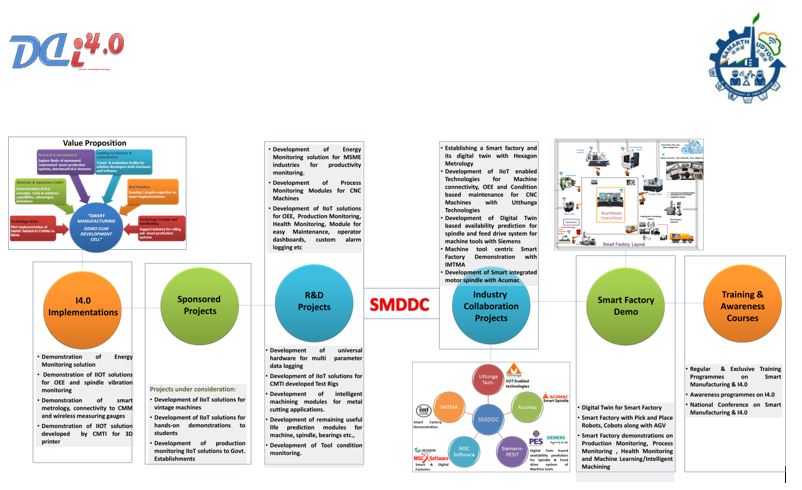
Centre Head | |||
Photo | Name | Designation | View Profile |
---|---|---|---|
![]() |
Mr. Prakash Vinod | Joint Director | View Profile |
Group Head | |||
Photo | Name | Designation | View Profile |
---|---|---|---|
Sorry, No Staff are Matched Your Criteria. |
Scientists | |||
Photo | Name | Designation | View Profile |
---|---|---|---|
![]() |
Mr. Girish Kumar M | Scientist - E | View Profile |
![]() |
Mr. Narendra Reddy T | Scientist - D | View Profile |
![]() |
Mr. Vithun S N | Scientist - D | View Profile |
![]() |
Mr. Harikrishna Satish Thota | Scientist - D | View Profile |
![]() |
Mr. Manjunath M A | Scientist - C | View Profile |
![]() |
Mr. Setti Suresh | Scientist - B | View Profile |
Technical Staff | |||
Photo | Name | Designation | Phone (Office) |
---|---|---|---|
![]() |
Mr. Mukunda M | Technical Assistant | 080-22188246 |
![]() |
Mrs. Lavanya R | Technical Assistant | 080-22188371 |
![]() |
Mr. Mehboob Basha | Technical Assistant | |
![]() |
Mr. Narasimharaju K V | Technician II |
Administration | |||
Photo | Name | Designation | Phone (Office) |
---|---|---|---|
Sorry, No Staff are Matched Your Criteria. |
- Technology Development for converting legacy machine tools to IIOT Smart Enabled Machine tools.
- Remote Monitoring of CNC machines @ CMTI into smart machines.
- Development of Low cost Energy Monitoring module for productivity enhancement for small scale industries.
- Development of Low cost Energy Monitoring module for productivity enhancement for smart factory.
- Development of a comprehensive machine tool health condition monitoring module
- Developmentof Supervisor login and OEE dashboard.
- Developments of module for tool wear monitoring using AI & ML techniques and OPCUA data.
- Extensive energy monitoring module with OEE evaluation for a smart factory.
- Technology development for smart spindle using AI & ML techniques.
- Development of IIOT solutions for Machine Tools to monitor the vibration, force, temperature and pressure.
- Development of industry 4.0 dashboard for Live Health Monitoring of Machines/Machine Tool Subsystem/Machine elements.
- Development of Smart Machine Health Trending and Analytics modules for Industry 4.0.
- Indigenous development of smart diagnostics module to achieve Zero Breakdown, productivity improvement and Prediction of impending problems.
- Development of Intelligent Data Analytics & Notification of remedial actions through SMS for Predictive maintenance.
- Development of Smart Motor Current Signature Analysis Module for Industry 4.0.
- Development of intelligent module to predict the Remaining Useful Life (RUL) of machine tools and its sub systems.
- Development of Digital Twin of Machine Tool Spindle.
- Development of Digital Twin for Feed Drive Systems.
Completed Projects
IOT Enabled “SMART” Metal Cutting Machine -empowering a Legacy Machine @CMTI
Smart features
Sensor modules
- Temperature : Machine thermal plot
- Vibration : Machine health
- Evaluate TcP(tool center point) drift
- Pressure : Spindle coolant pressure
- Energy : Downtime of the machine
- Vision : In-situ inspection / Quality
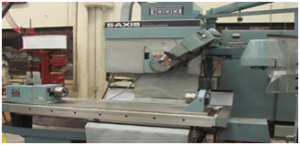



Outcome
- Generate diagnosis reports / action plan
- Classify reports based on severity
- Enable deep dive information for better process understanding
- Establish data base for further analytics
Outputs
- IOT enabled connected machine
- Remote access of machine health and process data
- Real time Machine health monitoring
- Energy monitoring
- Better process monitoring
- Reduced machine down time
Implementation: For the Demonstration of IOT Enabled Additive Manufacturing
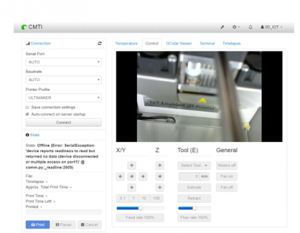
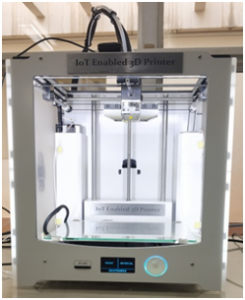
A IOT enabled Control GUI has been developed to control the 3D printer in a closed loop. The following features have been implemented.
- Cloud based 3D printing by uploading G-code via Any internet connected device, i.e Mobile Phones & Tablets.
- Cloud based closed loop monitoring of process parameters & Temperature signatures of subsystems of 3D printer.
- A complete live fabrication process can be viewed online via IOT process monitoring camera.
Ongoing Projects
Development of indigenous IIoT Solutions
Objective:
- Development of Production monitoring, Diagnostics and Condition
- Development of a Dashboard for Overall Equipment Efficiency
- Development of Low Cost Energy Monitoring IIOT Solution for Smart Factory
- Development of a compressive machine tool health condition monitoring module
- Development of Supervisor login and OEE dashboard
Outcome:
- Low cost IIoT Solutions for MSME’s
Smart Factory Demonstration
Objective:
- Establishment of Smart Factory Demonstration Cell at CMTI
Deliverables:
- Smart Factory Demonstration Cell at CMTI
Development of Production monitoring, Diagnostics and Condition Monitoring modules for machine tools
Objective:
- Development of IIOT solutions for Production Monitoring and OEE for Machine tool centric industries.
- Development of Diagnostics and Condition Monitoring module for machine tools.
Deliverables:
- IoT enabled vibration, temperature, force and pressure monitoring.
- Live Health Monitoring of Machines/Machine Tool Subsystem/Machine elements.
- Machine Health Trending and Analytics
- Technology Development, IP Creation
- Indigenous development of smart OEE & diagnostics module. Zero Breakdown, productivity improvement Prediction of impending problems.
Design and Development of Smart Precision Integrated Motor Spindle
Objective:
- Design and development of integrated motor spindle with in-built industry 4.0 features for machine tool application like HMC, VMC, ultra-precision machines
Deliverables:
- Smart spindles for High Precision HMC and VMC Machines.
- Integrated motor spindle with built in intelligent feature for building future smart machines.
- Technology Development, IP Creation
- Indigenous development and marketing
- Import Substitution
Digital Twin based Availability prediction for Spindle & Feed drive system of Machine tools
Objective:
- Development of Digital Twin based Availability Prediction for Spindle and Feed Drive systems of Machine Tools.
Outcome:
- Technology Development, IP Creation
- Smart Diagnosis and Prognosis Module of spindle and feed drive systems,
- Smart Inventory Management, Digital Twin based Production Availability Module, Production analytics Module
Establishment & Demonstration of Smart Factory with Digital Twin
Objective:
- To Establish and Demonstrate Smart factory and its digital twin for manufacturing industries
- To offer smart manufacturing solutions to industries
Outcome:
- To encourage SME’s. MSME’s to implement smart manufacturing technologies.
- Hands on experience and demonstration of smart manufacturing technology.
- Training of SME’s and MSME’s workforce.
Publications
- T Narendra Reddy, V Shanmugaraj, Prakash Vinod, Gopi Krishna S., “Real-time Thermal Error Compensation Strategy for Precision Machine tools”., Materials Today: Proceedings Volume 22, Part 4, Pages 2386-2396., 2020.
- Muhammed Nabil K M, Hare Prasaad P, Narendra Reddy T, Prakash Vinod, Senthil Kumar S, Thangavel S , Smart Factories – An Overview”, Manufacturing Technology Today, 2020
- Harikrishna Satish Thota, Naveen K, Ankit K, Balashanmugam N, “Design and development of dry microneedles electrode based portable wireless instrumentation system for EEG Acquisition. International Journal of Instrumentation Technology. Vol.2 No.2, 148-164, 2019
- Harikrishna Satish Thota, Naveen K, Ankit K, Balashanmugam N. “Design and Development of Dry Microneedles Electrode Based Portable Wireless Instrumentation System for EEG Acquisition”, International Journal of Instrumentation Technology, Inderscience Publications (Accepted)
- T Narendra Reddy, V Shanmugaraj, Prakash Vinod, Gopi Krishna S, S Narendranath., “Real-time thermal error compensation module for intelligent Ultra Precision Turning Machine (iUPTM)”., Procedia materials science, Volume 6, Pages 1981-1988, 2014.
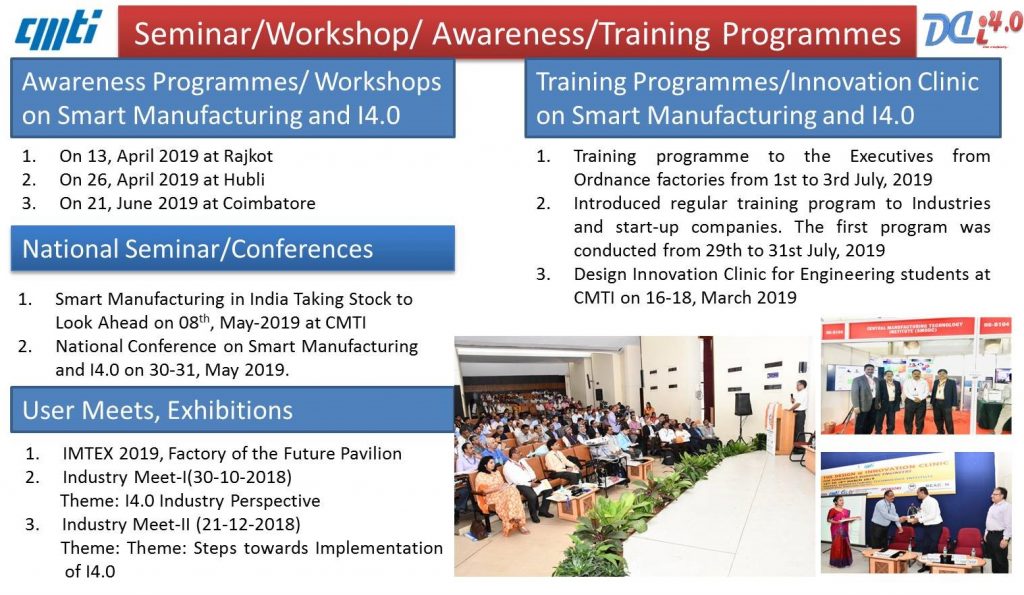
Mr. Prakash Vinod
Scientist-F & Centre Head –Smart Manufacturing,
Precision Machines Tools and Aggregates
Central Manufacturing Technology Institute (CMTI)
Tumkur Road, Bengaluru - 560022
Phone (office): +91-80-22188243, 23371516
Mobile: +91-9449842680
Fax: +91-80-23370428
E-mail: prakashv[at]cmti[dot]res[dot]in