- Introduction
- People
- Research Area
- Projects
- Facilities
- Achievements
- Gallery
- Contact Us
The Machine Vision group at the centre has been striving to achieve excellence in developing state of art technologies for non-contact inspection in the manufacturing domain. The group is working with various industry partners for providing targeted inspection solutions for in-line automated quality control applications as well as on futuristic research projects which can benefit the Indian industry in the long run. The vision technology team at CMTI has developed and successfully deployed solutions for several non-contact inspection requirements the latest one being an AI based solar panel inspection system named SolVIS at the plant of a leading manufacturer of solar panels. The system is capable of inspecting the solar panel EL images for presence and characterization of various categories of defects. The team has indigenously developed two technologies, fringe projection based and laser based, for 3D scanning of components. The fringe projection based scanning technology is able to 3D scan the components to an accuracy of 30 µm. It is a tripod mounted scanner with various options for view combining like marker based, optical tracker based, robot mounted etc. The laser based scanner developed in-house is designed for hand-held laser scanning. The device is capable of 3D scanning of intricate features by easily maneuvering the device over the object. The group is currently working on several projects for developing some cutting edge inspection technologies, most of them being, first time in the country. Some of these technologies are automated inspection methods for NDT applications, technologies for automated 3D inspection of PCBs and technology for closed loop control of build quality during fabrication of additive manufactured parts.
Centre Head | |||
Photo | Name | Designation | View Profile |
---|---|---|---|
![]() |
Mrs. Kusuma N | Scientist - E | View Profile |
Group Head | |||
Photo | Name | Designation | View Profile |
---|---|---|---|
Sorry, No Staff are Matched Your Criteria. |
Scientists | |||
Photo | Name | Designation | View Profile |
---|---|---|---|
![]() |
Mrs. Deepa R | Scientist - D | View Profile |
![]() |
Mr. Vinodh Venkatesh Gumaste | Scientist - C | View Profile |
![]() |
Mr. Bhavya Verma | Scientist - B | View Profile |
Technical Staff | |||
Photo | Name | Designation | Phone (Office) |
---|---|---|---|
![]() |
Mrs. Kavitha V | Senior Technical Assistant - I | 080-22188216/211 |
Administration | |||
Photo | Name | Designation | Phone (Office) |
---|---|---|---|
Sorry, No Staff are Matched Your Criteria. |
- Sub surface defect inspection systems.
- Deep Learning for inspection.
- Vision based closed loop process monitoring system.
- Embedded vision.
- 3D Scanning technologies based on Digital Fringe Projection (DFP) and laser scanning.
- In-situ inspection systems for quality control in factory lines.
1. Development of 3D Scanning Technologies by Digital Fringe Projection and Laser Scanning technologies
CMTI has experience in developing 3D scanners working on Digital Fringe Projection (DFP) and laser scanning technologies. The fringe projection based scanning technology is able to 3D scan the components to an accuracy of 30 µm. It is a tripod mounted scanner with various options for view combining like marker based, optical tracker (Developed by CMTI) based, robot mounted etc. The laser based scanner developed in-house is designed for hand-held laser scanning. The device is capable of 3D scanning of intricate features by easily manoeuvring the device over the object and is suitable for dark components scanning. These 3D scanners generate 3D model of a given component which is used in applications like 3D measurements, design evaluation, reverse engineering etc. 3D measurement technologies are highly in demand from industries and in various application domains.
-
Trikon-2 Hand-Held Laser Scanner


2. SolVIS: The AI Based Solar Panel Inspection Software
SolVIS is an inspection software for carrying out automated quality check on pre-captured EL images of onocrystallineand polycrystalline solar panel thereby providing characterization, reducing human error and stress and increasing efficiency of inspection.
Following are the distinctive features of the system:
- Defect detection and location marking.
- Defect characterization based on length and area.
- User defined dynamic inspection criteria.
- Inspection report with detailed defect statistics.
- Cycle time of 4 Secs/ panel.
- Option to train new panels.
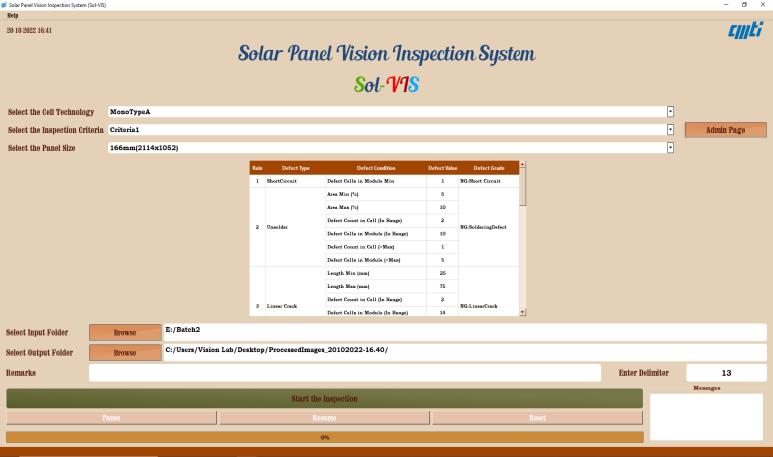

3. Thread measurement system

- Non-contact and improved method of external thread form parameter measurement to check for dimensional tolerances.
- High speed thread parameter measurement system which can be used for automating the thread measurement process in the thread manufacturing lines.
- User friendly thread measurement system requiring minimum human intervention.
- Records measurement results for statistical analysis.
3. Fluted Roller Vision Inspection system for defects.
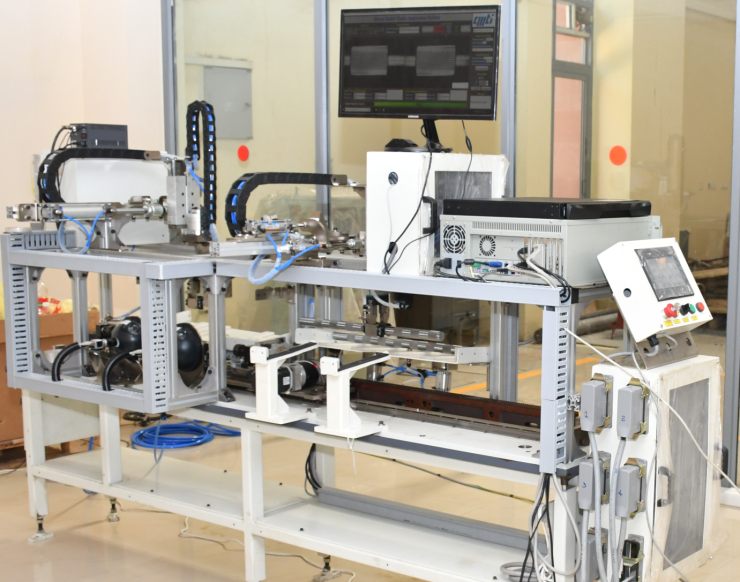
- The system is a vision based inspection system designed to inspect the fluted roller, used in textile machinery, for presence of chip-out and damages at before plating stage.
- The fluted roller vision inspection system consists of two sets of inspection units each unit consisting of a machine vision camera, optics and light sources.
- There are 8 variants in this component with variations in roller length, roller diameter, flute length and flute pitch.
- Various challenges like presence of oil on surface of the sample, reflective surface and variations in sizes and appearance are addressed in this project.
- The software has features like auto inspection cycle, manual inspection cycle, excel reporting eature, summary analysis report, model type detection, wrong loading detection in addition to the defect inspection feature.
4. Optical Tool Setter for USUPTM
- Optical tool setter is an accessory developed for performing the initial tool setting operation in the ultra precision turning machine, developed by CMTI. The system significantly reduce the tool setting time and also simplifies the process by providing accurate measurements of the tool tip offset and the tool nose radius.
5. Automated inspection of surgical screw
- The system is a non-contact inspection solution using machine
vision for Surgical Screws or Bone Screws. The inspection involves critical
dimensional measurement with very high accuracy for various parameters to be
inspected with different sizes and types of screws.
6. Automated inspection of drippers
- The system is a non-contact system for inspection of drippers.
Drippers are used in irrigation system. Different types of defects like hole blockage, flash on root and collar, cut on collar, short moulding and circularity of the drippers are inspected in this system.
7. Automated inspection of retaining bush.
- “Retaining bush” is a safety critical automotive plastic injection mould component.
- Able to identify all types of defects encountered in the component an inspection stations with 2 cameras
- Inspection rate of 3 components / sec
- Inspection also includes key dimensional measurements
- Automated Component feeding using a vibratory feeder.
- Range of Cameras to cater highly accurate measurements, high speed inspection and Defect Identification in the Visible and Infrared regions.
- Different types of Lightings to cater to components of varied colors and reflectivity.
- High Precision Optics like Telecentric , High Resolution and High Speed lenses
- Brightfield Microscope with Nano Positioning Stages
- Software tools for Automation Solutions and Image Processing.
Patent: System and Method for Thermal Error Compensation in Machines using Vision Measurement.
Copyrights:
- Thread Measurement System TMS-030
- Optical Tool Set Station – OpToSS
Award:
“Best Paper” award for paper titled “Development of Automated Vision Inspection System for Two Wheeler Engine Crankshaft” presented at the 4th National Conference on Advances in Metrology AdMet-2015 under the session “Dimensional Measurement and Machine Vision”.
Publications:
- Pavan Kumar Asundi & Deepa, ‘Interference Fringe-Based Metrology for Industrial Applications’, Advances in Modelling and Optimization of Manufacturing and Industrial Systems, Feb 2023, pp 511–521.
- Vinodh Venkatesh Gumaste, Deepa R., Vidya Kumari K. R., Kavitha V, ‘Optical Tracking System for Auto-Registration of Multiple Views of a 3D Scanner for 3D Shape Reconstruction of Components’, 2nd IEEE International Conference on Emerging Frontiers in Electrical and Electronic Technologies (ICEFEET- 2022).
- Maithreyan G, Vinodh Venkatesh Gumaste, ‘Comparison of various Machine Learning and Deep Learning classifiers for the classification of Defective Photovoltaic cell’, International Conference on Robotics, Control, Automation and Artificial Intelligence (RCAAI) 2022.
- Pavan kumar A, Deepa R, Kavitha V, ‘Evaluation of Stereo Camera Calibration for Metrology Applications’, First International Conference on “Recent Trends in Electrical, Electronics, Communication and Instrumentation" (ICRTEECI 2021).
- Deepa, V. Kavitha, ‘IOT Enabled Part Quality Check Using Vision’, International Journal of Imaging & Robotics (ISSN 2231-525X), 2020, Volume 20, Issue Number 1, pp 44-52.
- Deepa, R. Madhusudhan Rao, S. Usha, J. Pradyumna (2019), ‘Development of 3D Scanning system by Digital Fringe Projection’, International Journal of Imaging & Robotics, 2019, Volume 19, Issue Number 1, pp 117-130.
- , Deepa Radhakrishna, Usha S (2018), ‘Development of a Robot-mounted 3D Scanner and Multi-view Registration Techniques for Industrial Applications’, Procedia Computer Science, Volume 133, 2018, pp. 256-267.
- Madhusudhan Rao R, Deepa R, Kavitha V, Usha S(2016), ‘A Fast, Reliable Fringe Projection Profilometry System’, Manufacturing Technology Today, Volume 15, Issue 1, pp 3-11.
- Deepa, J.Pradyumna, S.Harsha, S.Usha (2015), ‘Development of Automated Vision Inspection System for Two Wheeler Engine Crankshaft’, MAPAN, Journal of Metrology Society of India, December 2015, Volume 30, Issue 4, pp 273–280.
- Harsha, R. Deepa, V. Kavitha, S. Usha, Vision based surgical screw inspection, Advances in Metrology - ADMET 2015.
- R Deepa, S Usha, P V Shashi Kumar (2014), ‘Automated vision inspection system for a plastic injection mould component’, Advanced Materials Manufacturing and Characterisation, March 2014, Volume 4, Issue 1, pp 26-31.
- R Deepa,S Usha, P V Shashi Kumar, Automated vision inspection system for a plastic injection mould component, All India Manufacturing Technology Design and Research Conference - AIMTDR 2014.
- R. Deepa, S. Usha, P. Babin, ‘Innovative Algorithm for External Thread Measurement using Machine Vision’, International conference on precision, meso, micro and nano engineering - COPEN 2011.
- S.Usha, R.Deepa, P.V.Shasikumar , Dr.G.C. Mohankumar, Through Focus Imaging Technique for Nano Scale Dimensional Analysis, International conference on precision, meso, micro and nano engineering - COPEN 2011.
Book Chapter :
- “Factors affecting the accuracy of a laser scanner”, Pavan kumar A, Deepa R, Kavitha V,
Book Name: Computer Vision Applications of Visual AI and Image Processing published by DE GRUYTER, Berlin, Germany, 2023, Vol 15, pp 327-354.
Mrs. Kusuma N
Centre for Sensors, Vision Technology and IT
Central Manufacturing Technology Institute (CMTI)
Tumkur Road, Bengaluru - 560 022
Phone (Office): +91-80-22188349
Mobile: +91-9449842664
Fax: +91-80-23370428
Email: kusuma[at]cmti[dot]res[dot]in
Mrs. Deepa R
Group Head for Vision Technology
Central Manufacturing Technology Institute (CMTI)
Tumkur Road, Bengaluru - 560 022
Phone (Office): +91-80-22188329
Mobile: +91-9449842667
Fax: +91-80-23370428
Email: kusuma[at]cmti[dot]res[dot]in