- Introduction
- People
- Projects
- Services
- Facilities
- Contact
India is developing at a mind-boggling pace, with its strategic place as one of the world’s largest economies, it is in dire need of reliance on indigenous technologies.
CMTI’s Centre for additive and special manufacturing (C-ASMP) is a cluster of teams with a specific focus on Prototyping, product and testing
technologies which cater to the very need as discussed.
Core Competencies of C-ASMP are,
- Additive manufacturing
- Manufacturing processes of special products
- Hydraulic and Pneumatic systems
- Aerospace test rig and calibration
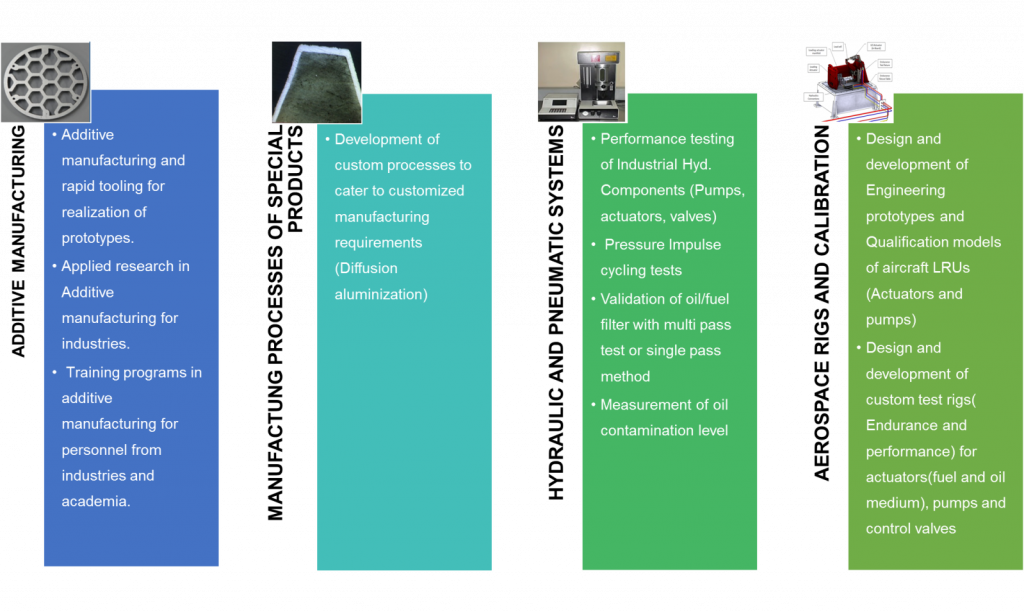
Centre Head | |||
Photo | Name | Designation | View Profile |
---|---|---|---|
![]() |
Mr. Shanmugaraj V | Joint Director | View Profile |
Group Head | |||
Photo | Name | Designation | View Profile |
---|---|---|---|
Sorry, No Staff are Matched Your Criteria. |
Scientists | |||
Photo | Name | Designation | View Profile |
---|---|---|---|
![]() |
Mr. Vinay Kumar P V | Scientist - D | View Profile |
![]() |
Mr. Deepak Singh D | Scientist - C | View Profile |
![]() |
Mrs. Shruthi G | Scientist - D | View Profile |
Technical Staff | |||
Photo | Name | Designation | Phone (Office) |
---|---|---|---|
![]() |
Mr. Manju M | Senior Technical Assistant - I | 080-22188352 |
![]() |
Mr. Girisha C V | Technical Assistant | 080-22188239 |
![]() |
Mr. Prakash V S | Technician III | 080-22188318 |
![]() |
Mr. Tharanatha P | Technician III | 080-22188239 |
Administration | |||
Photo | Name | Designation | Phone (Office) |
---|---|---|---|
Sorry, No Staff are Matched Your Criteria. |
Testing of Hydraulic elements
Sl. No. | Name & Specifications | Photo |
---|---|---|
1 | Impulse Pressure Test of Retraction Actuator (RA PT-01) for Rustom II – UAV i. Testing as per MIL-PRF-5503F. |
![]() |
2 | Performance test on centrifuge for Alfa laval
|
![]() |
3 | Pressure Impulse Test on Ti Tubes Pressure impulse testing of indigenous Ti-Tubes as per SAE ARP 1383. |
![]() |
4 | Pressure Impulse test on Hydraulic cylinders (Pricol) i. No of Cylinders: 6 nos. |
![]() |
Other Misc. Testing
- Onsite performance testing of the centrifugal separator developed by M/s Alfa Laval India Pvt. Ltd, Pune, and M/s GEA Westphalia Separators India Pvt. Ltd., Bangalore.
- Test setup for pressure cycling of the parker filters at 40°C and 80°C, and filter assembly for its fatigue strength test. Pressure cycling tests on hydraulic filters were carried out for 0-8 bar at 5Hz for Parker Hannifin.
- Hot soak and Cold soak of hydraulic cylinders for 24 hrs and performance test on hydraulic cylinders for Wipro Ltd.
- Drum Top Filtration unit was tested by the portable particle counter for its performance for Tri-Millennial Design and Service Engineers Pvt. Ltd.
- Flow Fatigue test of the Hydraulic filters was carried out for 9 bar differential pressure at 1Hz for Micro Precision
- Burst pressure testing of Welded D-Tube and Pressure drop and thermal efficiency test of a cold plate for RangsonsDefense Solution Pvt. Ltd, Bangalore
- Static Pressure testing (pneumatic) of 105 nos. fire extinguisher cylinders of Southern Electronics Pvt. Ltd., Bangalore Pressure drop test and burst pressure testing of Direction control valves, Dynamatic Technologies Ltd, Bangalore
- Performance test on Avionic cold plate was carried out with test fluid, Poly Alfa Olephin (PAO) at 60 °C and flow rate 0.7 GPM for Ranson defence solutions.
- Single-pass performance testing on Filter elements for Gopani Product Systems.
- Filtration efficiency test and dirt holding capacity test on Spin-on filters were taken up and completed for BEML Mysore, Parker Hannifin, Ind Auto filters, Sany Heavy Industries India Pvt. Ltd., Ultrafilter (India) Pvt. Ltd., Micro Precision, Micropore.
- Total no of filters tested for efficiency: 112nos
- Total no of filters tested for pressure cycling: 11nos
- Testing services in the field of Industrial Hydraulic Elements.
- Performance Test of Industrial pumps, control valves, cylinders etc
- Thermal Performance test, Endurance test, ageing test, thermal shock test etc.
- Characterization of Industrial hydraulic elements.
- Hydrostatic pressure testing.
- Pressure cycling test on hydraulic elements.
- Cold / hot soak and performance test on hydraulic elements.
- Validation of oil/fuel filter performance by Multi-pass or single pass method, dirt holding capacity, collapse rating etc.
- Laboratory services.
- Measurement of oil contamination level by particle count (ISO 4406 & NAS 1638)
- Component cleanliness level checking
- Calibration of Pressure gauges.
- Supply of calibration fluid
- Supply of ultra-clean bottles
- Tank capacity : 800 l
- Oil : ISO VG 46
- Max. Flow rates: 95lpm (pump test stand)
100 lpm (Cylinder and valves test stand) - Operating pressure: up to 210 bar
- Heat removal rate: up to 30000 kcal\hr
- Performance testing of pumps, valves and cylinders
Mr. Deepak Singh D (Scientist-B)
Email: deepak[at]cmti[dot]res[dot]in
Land Line: +91-80-22188215
Mr. S K Verma(Scientist-F & CH – (C-ASMP) & GH (ES))
Email:vermask[at]cmti[dot]res[dot]in
Land Line: +91-80-22188325
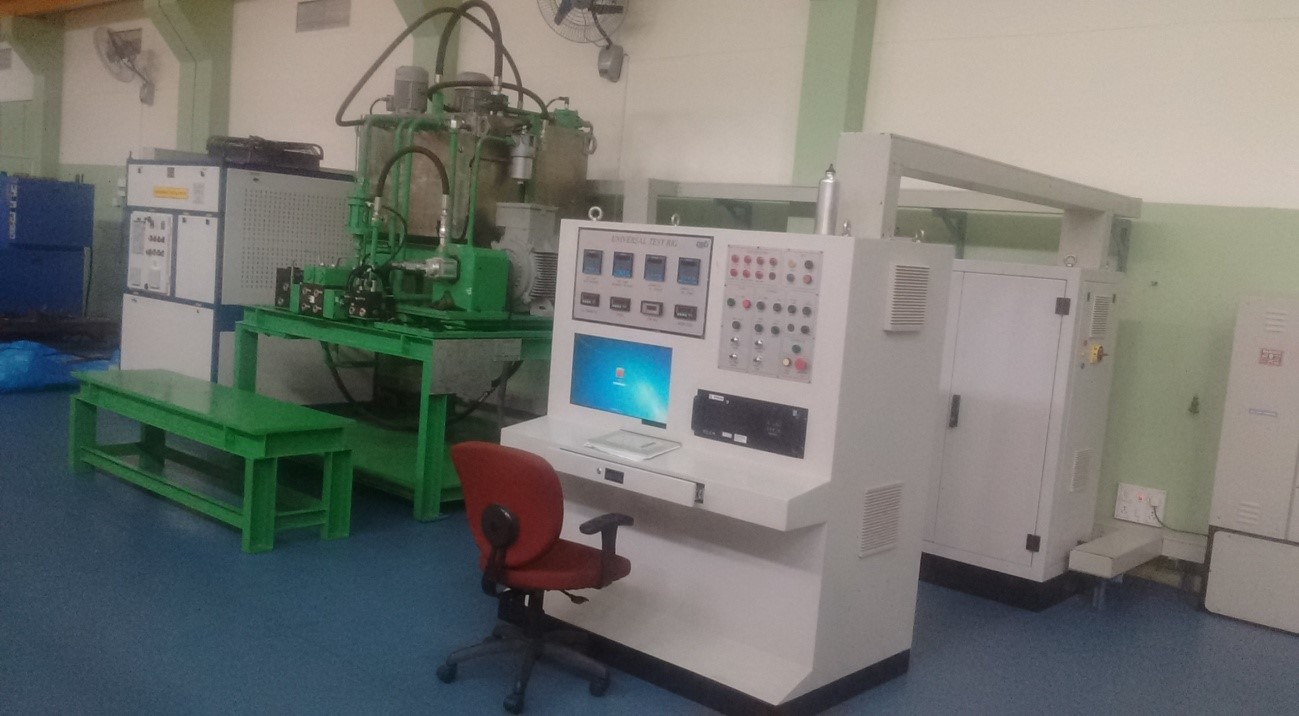
- Fluid Medium: Air/ MIL-PRF-5606H
- Pressure: upto 15bar(with air) and upto 1000bar (with oil)
- Standard followed: ISO 4548-6 (Burst pressure test) & AS 21902 (Proof pressure test)
- A pressure test to determine the ability of the component to withstand a static pressure and to determine the pressure at which it fails. It is done both hydraulic and pneumatically. We can pressurise the test unit using a handpump/ radial piston pump.
Mr. Deepak Singh D (Scientist-B)
Email: deepak[at]cmti[dot]res[dot]in
Land Line: +91-80-22188215
Mr. S K Verma(Scientist-F & CH – (C-ASMP) & GH (ES))
Email: vermask[at]cmti[dot]res[dot]in
Land Line: +91-80-22188325
- Standard followed – ISO 4406, NAS 1638
1. Automatic Bottle Sampler
2. Eight Channel Particle Counter - Particle size: 4, 6, 14, 21, 38, and 70 µm (As per ISO Standard)
- Offline method for defining the contamination level based on the number and size of particles in the given fluid. It requires a sampler and a particle counter.
Mr. Deepak Singh D(Scientist-B)
Email: deepak[at]cmti[dot]res[dot]in
Land Line: +91-80-22188215
Mr. S K Verma(Scientist-F & CH – (C-ASMP) & GH (ES))
Email: vermask[at]cmti[dot]res[dot]in
Land Line: +91-80-22188325
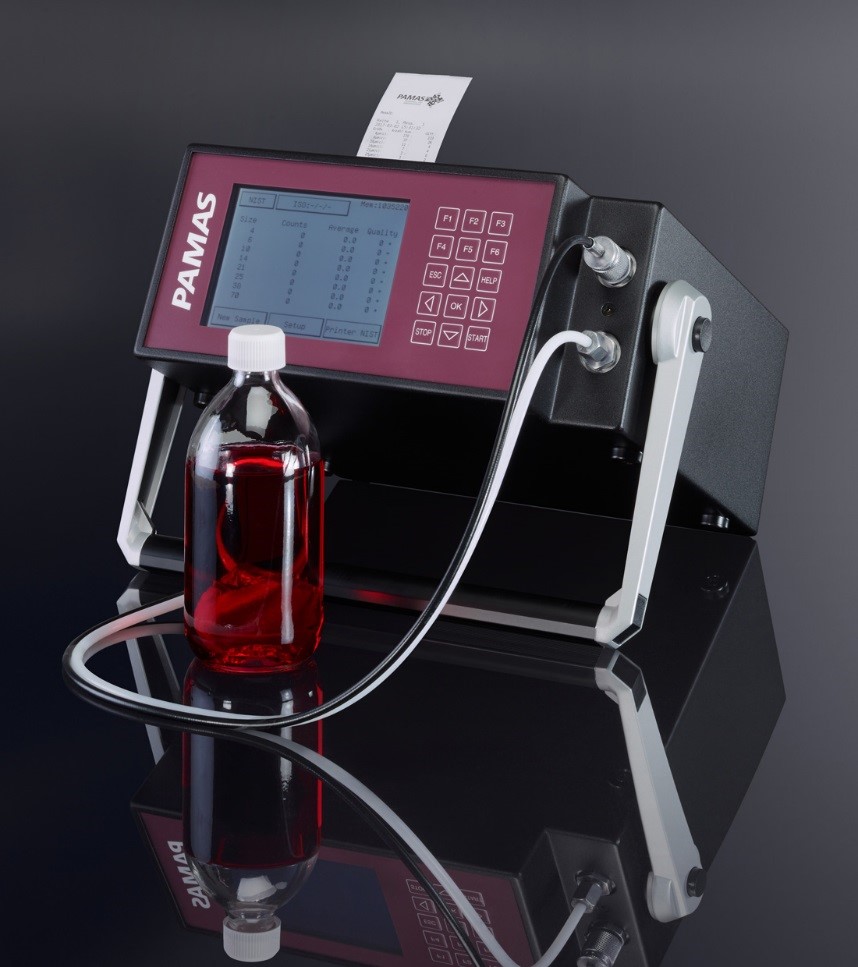
- Standard followed – ISO 4406, NAS 1638
- Automatic Bottle Sampler
- Eight Channel Particle Counter
- Particle size: 4, 6, 14, 21, 38, and 70 µm (As per ISO Standard)
- Offline method for defining the contamination level based on the number and size of particles in the given fluid. It requires a sampler and a particle counter.
Mr. Deepak Singh D (Scientist-B)
Email: deepak[at]cmti[dot]res[dot]in
Land Line: +91-80-22188215
Mr. S K Verma(Scientist-F & CH – (C-ASMP) & GH (ES))
Email: vermask[at]cmti[dot]res[dot]in
Land Line: +91-80-22188325
- Fluid Medium: Petroleum ether (filtered with 0.8μm filter membrane)
- Filter membrane used:
a) Material – Cellulose
b) Thickness – 5 μm - Standard followed: ISO 4405
- Patch method for defining the contamination level based on the number of contaminant particles in the given fluid or we can clean the component with filtered IPA/petroleum ether, collect the residue and pass it thru a membrane to estimate the contamination level in terms of mg of contaminant, also we can collect the membrane and send it for microscopic /spectrometric/particle size analyser for further analysis.
Mr. Deepak Singh D (Scientist-B)
Email: deepak[at]cmti[dot]res[dot]in
Land Line: +91-80-22188215
Mr. S K Verma (Scientist-F & CH – (C-ASMP) & GH (ES))
Email: vermask[at]cmti[dot]res[dot]in
Land Line: +91-80-22188325
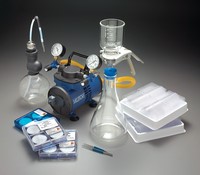
- Pressure range: ± 2 psi
- Fluid used: Iso-Propyl Alcohol (IPA)
- Filter element dimensions: upto 100mm diameter and 300mm long
- Standard followed: ISO 2942
- Bubble Point method used both to verify the fabrication integrity of the filter element (by checking the absence of bubbles) and to zero in on the location of largest pore of the filter element.
Mr. Deepak Singh D (Scientist-B)
Email: deepak[at]cmti[dot]res[dot]in
Land Line: +91-80-22188215
Mr. S K Verma(Scientist-F & CH – (C-ASMP) & GH (ES))
Email: vermask[at]cmti[dot]res[dot]in
Land Line: +91-80-22188325
- Max Flow rate : 300 lpm
- Temperature: Ambient temperature to 70 deg C
- Max Differential Pressure:35 bar
- Particle Counter: PAMAS Detection range 4 to 70 microns
- Max Concentration: 1, 20, 000 Particles/ml
- Pressure range: 7 to 8 bar max
- Standards followed: ISO Standard 4548-12:2017E (Oil Filters)
- ISO Standard 16889: 2008 (Hydraulic Filters)
- ISO Standard 19438:2003E (Fuel Filters)
- Clean Element Pressure drop Test
- Collapse Pressure Test
- Bypass Valve opening/closing Test
- Pressure cycling test
- Flow fatigue test
- Proof/burst pressure test of the filter assembly.
Mr. Deepak Singh D (Scientist-B)
Email: deepak[at]cmti[dot]res[dot]in
Land Line: +91-80-22188215
Mr. S K Verma (Scientist-F & CH – (C-ASMP) & GH (ES))
Email: vermask[at]cmti[dot]res[dot]in
Land Line: +91-80-22188325

Mr. Shanmugaraj V
Centre Head for Aerospace System Group(AS) and Additive Manufacturing Group(AM)
Phone (Office): +91-80-22188349
Mobile: +91-9449842688
Fax: +91-80-23370428
E-mail: shanmugaraj[at]cmti[dot]res[dot]in